What Does OSHA Stand For: A Comprehensive Guide To Workplace Safety
OSHA stands for Occupational Safety and Health Administration, a federal agency in the United States dedicated to ensuring safe and healthy working conditions for all employees. Established under the Occupational Safety and Health Act of 1970, OSHA plays a pivotal role in regulating workplace safety standards and protecting workers from hazards. Understanding OSHA's role is crucial for employers and employees alike, as it directly impacts workplace safety and compliance.
Workplace safety is not just a regulatory requirement but a moral obligation for organizations. OSHA's mission is to prevent work-related injuries, illnesses, and deaths by setting and enforcing protective standards. By adhering to OSHA guidelines, businesses can create a safer environment for their employees, leading to increased productivity and reduced costs associated with accidents.
This article aims to provide an in-depth understanding of OSHA, its significance, and its impact on workplace safety. Whether you're an employer, employee, or safety professional, this guide will equip you with the knowledge needed to navigate the complexities of OSHA compliance and foster a culture of safety in your organization.
Read also:Jackerman Mother Warmth Chapter 3 Unveiling The Depths Of Emotional Connection And Growth
Table of Contents
- The History of OSHA
- OSHA's Mission and Objectives
- OSHA Standards and Regulations
- Enforcement of OSHA Standards
- OSHA Training Programs
- OSHA Inspections and Compliance
- Employee Rights Under OSHA
- Benefits of OSHA Compliance
- Challenges in Implementing OSHA Standards
- The Future of OSHA
The History of OSHA
OSHA was established on December 29, 1970, when President Richard Nixon signed the Occupational Safety and Health Act into law. The act was created in response to growing concerns about workplace safety and health in the United States. Prior to OSHA, there were no comprehensive federal regulations to protect workers from hazards such as toxic chemicals, unsafe machinery, and hazardous working conditions.
Key Milestones in OSHA's History
- 1971: OSHA establishes its first standards for general industry, construction, and maritime sectors.
- 1983: OSHA introduces the Hazard Communication Standard (HCS) to ensure workers are informed about chemical hazards.
- 2010: The passage of the Occupational Safety and Health Act's Whistleblower Protection Program strengthens protections for workers who report unsafe conditions.
Since its inception, OSHA has evolved to address emerging workplace hazards and incorporate advancements in technology and industry practices. Its history reflects a commitment to improving workplace safety and protecting workers' rights.
OSHA's Mission and Objectives
The mission of OSHA is to "assure safe and healthful working conditions for working men and women by setting and enforcing standards and by providing training, outreach, education, and assistance." This mission is supported by several key objectives:
- Set enforceable standards to protect workers from recognized hazards.
- Enforce compliance through inspections, penalties, and citations.
- Provide training and education to employers and employees on workplace safety practices.
- Promote voluntary compliance programs to encourage proactive safety measures.
OSHA's objectives are designed to create a balanced approach to workplace safety, combining regulatory enforcement with education and collaboration. By achieving these objectives, OSHA aims to reduce workplace injuries, illnesses, and fatalities.
OSHA Standards and Regulations
OSHA standards are legally enforceable rules that employers must follow to ensure workplace safety. These standards cover a wide range of industries and hazards, including general industry, construction, maritime, and agriculture. OSHA standards are categorized into several groups:
Types of OSHA Standards
- General Industry Standards: Covering workplace hazards common to most industries.
- Construction Standards: Addressing safety concerns specific to construction sites.
- Maritime Standards: Regulating safety in shipyards, marine terminals, and longshoring operations.
- Agriculture Standards: Protecting workers in farming, forestry, and other agricultural activities.
OSHA standards are regularly updated to reflect new research, technology, and industry practices. Employers are required to stay informed about these updates and implement necessary changes to maintain compliance.
Read also:Capital One Pay By Phone Number A Comprehensive Guide To Simplify Your Payments
Enforcement of OSHA Standards
OSHA enforces its standards through inspections, citations, and penalties. Inspections can be triggered by several factors, including employee complaints, referrals, and random selection. During an inspection, OSHA compliance officers evaluate workplace conditions, review safety records, and interview employees.
Steps in the OSHA Inspection Process
- Opening Conference: Discussing the purpose and scope of the inspection with the employer and employee representatives.
- Worksite Walkaround: Inspecting the workplace for hazards and violations.
- Closing Conference: Reviewing findings and discussing potential citations or corrective actions.
Employers found in violation of OSHA standards may face fines, penalties, or other legal consequences. However, OSHA also provides resources and assistance to help employers achieve compliance and improve workplace safety.
OSHA Training Programs
Training is a critical component of OSHA's mission to promote workplace safety. OSHA offers various training programs designed to educate employers and employees about safety standards, hazard recognition, and prevention strategies.
Popular OSHA Training Programs
- OSHA 10-Hour and 30-Hour Training: Providing foundational knowledge for workers and supervisors in general industry and construction.
- Outreach Training Program: Offering courses on specific safety topics, such as fall protection and electrical safety.
- Voluntary Protection Programs (VPP): Recognizing employers who go above and beyond OSHA standards to create exceptional safety cultures.
By participating in OSHA training programs, employers and employees can enhance their understanding of workplace safety and develop the skills needed to prevent accidents and injuries.
OSHA Inspections and Compliance
OSHA inspections play a vital role in ensuring compliance with safety standards. Employers are required to maintain accurate records of workplace injuries and illnesses and make them available for review during inspections. Compliance with OSHA standards is not optional; it is a legal obligation that carries significant consequences for non-compliance.
Best Practices for OSHA Compliance
- Conduct regular safety audits to identify and address potential hazards.
- Train employees on safety procedures and emergency response protocols.
- Document all safety-related activities, including training sessions and incident reports.
Employers who prioritize OSHA compliance not only protect their employees but also enhance their organization's reputation and bottom line. A safe workplace is a productive workplace.
Employee Rights Under OSHA
OSHA guarantees certain rights to employees to ensure they can work in a safe and healthy environment. These rights include the right to file a complaint, request an inspection, and receive information about workplace hazards.
Key Employee Rights Under OSHA
- Right to a safe workplace free from recognized hazards.
- Right to file a confidential complaint with OSHA.
- Right to participate in OSHA inspections and receive inspection results.
OSHA also protects employees from retaliation for exercising their rights. Employers are prohibited from discriminating against or punishing employees who report unsafe conditions or participate in OSHA activities.
Benefits of OSHA Compliance
Compliance with OSHA standards offers numerous benefits to employers and employees. Beyond the moral and legal obligations, there are tangible advantages to maintaining a safe workplace.
- Reduced workplace injuries and illnesses lead to lower healthcare costs and workers' compensation claims.
- Improved employee morale and productivity result from a safer and healthier work environment.
- Enhanced reputation and competitive advantage attract top talent and customer loyalty.
By prioritizing OSHA compliance, organizations can create a positive workplace culture that values safety and well-being.
Challenges in Implementing OSHA Standards
While OSHA standards are essential for workplace safety, implementing them can present challenges for employers. Common obstacles include limited resources, lack of awareness, and resistance to change. However, these challenges can be overcome with proper planning and support.
Strategies to Overcome OSHA Implementation Challenges
- Allocate sufficient budget and resources for safety programs and training.
- Engage employees in the safety process through communication and collaboration.
- Utilize OSHA resources and partnerships to gain expertise and guidance.
By addressing these challenges proactively, employers can ensure successful implementation of OSHA standards and achieve their safety goals.
The Future of OSHA
As industries evolve and new hazards emerge, OSHA continues to adapt its standards and strategies to meet the changing needs of the workforce. The future of OSHA lies in leveraging technology, data analytics, and collaboration to enhance workplace safety.
- Advancements in technology, such as wearable devices and IoT, offer new opportunities for monitoring and preventing hazards.
- Data-driven approaches enable more targeted inspections and interventions, maximizing OSHA's impact.
- Partnerships with industry stakeholders foster innovation and shared responsibility for workplace safety.
By embracing these advancements, OSHA can continue to lead the charge in protecting workers and promoting safe workplaces for generations to come.
Conclusion
In conclusion, understanding what OSHA stands for is crucial for anyone involved in the workplace. OSHA plays a vital role in ensuring safe and healthy working conditions for all employees through its standards, enforcement, and educational initiatives. By adhering to OSHA guidelines, employers can create a safer environment that benefits both their workers and their business.
We encourage you to take action by reviewing your workplace safety practices, participating in OSHA training programs, and staying informed about updates to OSHA standards. Share this article with your colleagues and explore other resources on our site to further enhance your knowledge of workplace safety. Together, we can make a difference in protecting workers and promoting a culture of safety.
References:
- Occupational Safety and Health Administration (OSHA) website
- U.S. Department of Labor
- National Institute for Occupational Safety and Health (NIOSH)
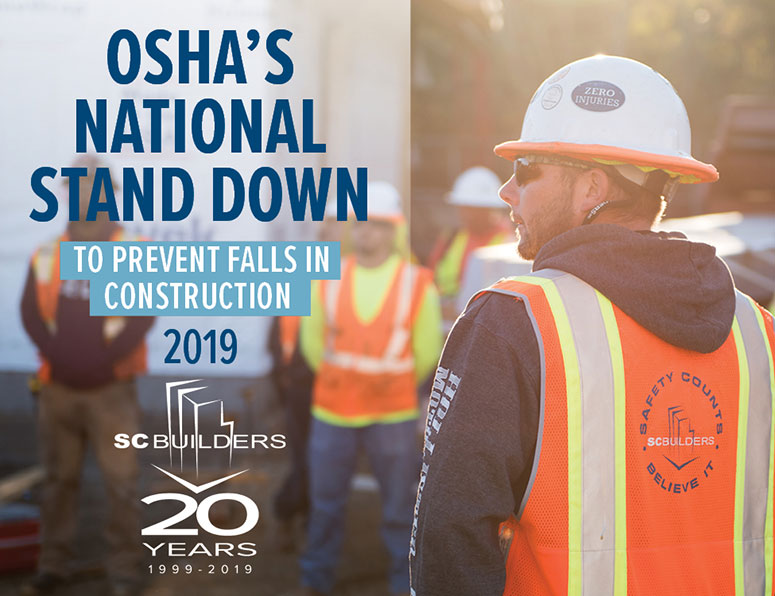

